Holo3 Polymap
1. Introduction
Holo3 is a technology transfer center specializing into imaging and optical methods and located in St Louis ( France ). They develop and make available to industries optical ressources on different forms, such as feasibility studies, tailored services with their own equipments or specific measure method supplies.
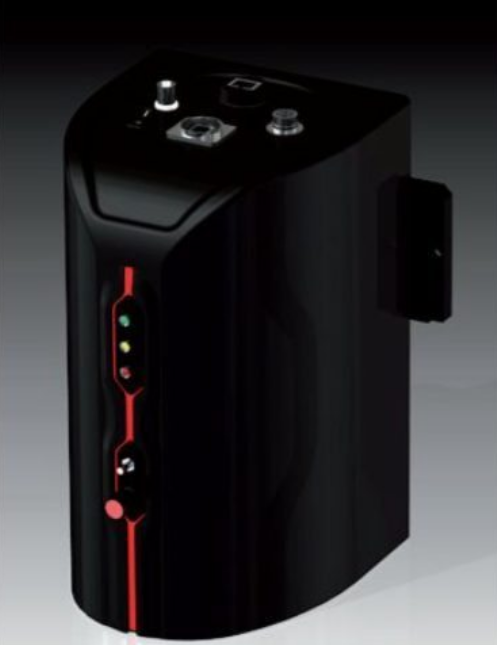
Among all this activities stand Polymap, a device born from the collaboration between Holo3 and the Institut Charles Sadron ( Strasbourg, France ).
To study the self-healing property after surface damage (such as scratching) of some viscoelastic polymers, the precise measurement of the surface micro-geometry is needed. Polymap is an innovative non-invasive and fast device created to do those precise measurement even on opaque materials.
It can be used to measure local slopes of a surface, by using deflectrometry principle, in order to reconstruct it in 3D. It also have the capacity, as a result of its high sensibility, to measure prints on the study surface, about the micron size. Furthermore, the measures are done in a short time laps, without any specific preparations to do.
1.1. Challenges and Goals
The project presented here follows on an previous internship with the Master CSMI realised in 2015. The main goal consists of reconstructing, from the slopes obtained by the Polymap device, the associated surface with the Finite Element method. At this task, we can add the possibility to take in account initial conditions, height mean of the surface for example, to work on an irregular mesh, due to camera deformations, or to exclude automatically areas with non compliant, or even nonexistent, data.
1.2. Mathematical and computational methods
During this project, we developed two main applications for Holo3 :
-
The surface reconstruction application use for a unique set of data
-
The serial control application to solve our surface reconstruction problem with numerous sets of data at the time.
These applications has been optimized trough modifications to take the least ammount of time to run, such as the full parallelization of codes, new mesh objects dedicated to this problem ( uniform and deformed ), or testing which preconditionner/solver in Feelpp suits the most in this case. The modifications don’t stop to time gain but come also with new features, like the extraction and deletion of mesh areas we suspect to contain false data value with polygon definition.